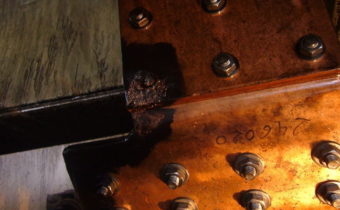
Application of passivators in transformer insulating mineral oils
Abstract Electrical insulating mineral oils are mainly manufactured from naphthenic crude sources, with a small number being produced from paraffinic crudes and gas-to-liquids technology. The...
by Lance Lewand
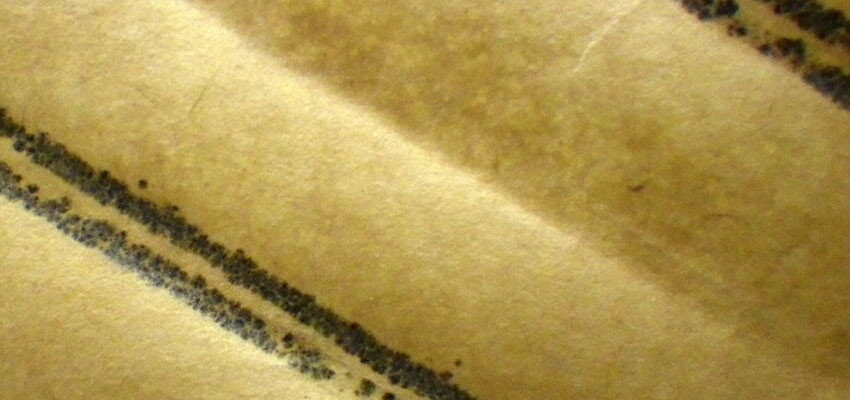
Abstract
Electrical insulating mineral oils are mainly manufactured from naphthenic crude sources, with a small number being produced from paraffinic crudes and gas-to-liquids technology. The resulting products are most frequently free of additives, except for certain types of phenol-based oxidation inhibitors, and of a very low percentage by weight, only up to 0.4 %. The main specifications for electrical insulating oils, Doble TOPS, ASTM D3487 and IEC 60296, only allow oxidation inhibitors and any other additives must be agreed upon by the entities involved in the selling and purchasing of the product. Over the years, other additives have been used, sometimes unbeknownst to the purchaser, some of which include pour point depressants, gassing tendency additives, other types of oxidation inhibitors, passivators and metal deactivators. This paper discusses the uses of passivators and how they work in transformer systems. Presently, passivators are being used to control issues with corrosive sulfur but they have also been used to control oxidation stability of the oil and streaming (static) electrification. This paper will focus mainly on the use of passivators to control corrosive sulfur.
Keywords: passivators, benzotriazole, BTA, Irgamet 39, Irgamet 30, corrosive sulfur, copper sulfide, transformer oil, insulating mineral oil
Introduction
Since about 1996, the electric power industry has seen a rash of failures of large power transformers, shunt reactors, load tap changers and bushings due to conditions caused by corrosive sulfur compounds in electrical insulating oil. This was a worldwide phenomenon with the Brazil electric system being the most severely impacted. The phenomenon is not new and has been known since the early 1930s. Up until the 2000 time frame, the failures due to corrosive sulfur were sporadic and manageable. However, from 2000 through 2007, the rash of failures was so prevalent that several utilities were concerned with reliability on their system. As a percentage of the total population of transformers the failure rate attributed to corrosive sulfur is still very small but impactful.
Transformers are large industrial machines that are basically handmade, take many months to build and cost millions of US dollars, are specific to a utility system and cannot be easily replaced. Transformers are designed and built to last 20 years or more at nameplate rating with many of them operating over 40 years. The corrosive sulfur failures in recent years involved relatively new electric apparatus, most less than 10 years old and some with less than a year in service. Spare transformer policies in place during the 1990s and early 2000s, as a result of utility deregulation in the United States and other parts of the world, in some cases reduced available spares. Thus, replacements for failed transformers were not available and compounded the issue. Those policies have since been revisited and the amount of spare transformers available has been readjusted.
Transformers vary in size but large units can hold from 35,000 to 100,000 liters or more of electrical insulating oil and large quantities of core steel, copper, electrical insulating paper and pressboard, among other components. The total weight of these materials can be several hundred tons when finally installed. None of these internal components were meant to be changed out over the life of the transformer. Failures of transformers due to corrosive sulfur compounds occur because they react with the copper conductor in the transformer windings, lead assemblies and silver components that can progress into several different failure modes. Three failure modes are the most common.