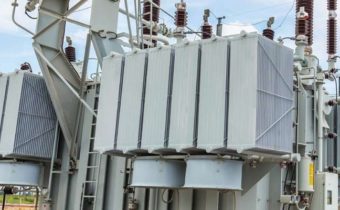
Editorial message
Dear Readers, One of the important practices of influential companies is that they always observe and consider technological and market trends, following current developments, forecasting...
by Mladen BANOVIC
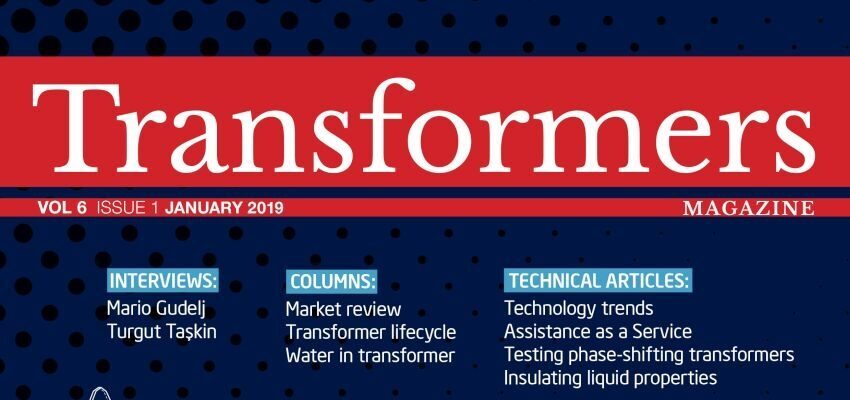
Dear Readers,
One of the important practices of influential companies is that they always observe and consider technological and market trends, following current developments, forecasting future needs and requirements, and planning and preparing for the pending changes. The same is true for the companies in our industry. However, over the past few years we’ve been witnessing a trend where even middle-sized and some relatively small companies are beginning to understand the importance of following the trends, making timely plans for the expected future circumstances. While some trends emerge due to technical reasons, there are also trends that develop as a result of new regulations, one example being the so-called eco-design regulation for various electrical devices, including power transformers.
I have recently had an honour to preside over a Plenary Session of My Transfo 2018, the ninth edition of the Oil & Transformer Conference held in Turin, Italy. While the main focus of this conference is transformer oils, other transformer-related topics are also discussed, particularly those that concern smart and environmentally-friendly solutions. This year, we reflected on eco-design (low-loss) transformers that are coming into use in line with the requirements of the Eco-Design Regulation implemented in the EU. The objective of this Regulation is to ensure that the power transformers placed on the EU market will result in energy savings and reduce CO2 emissions throughout their service lives, in a cost-effective manner. Similar regulations exist in other markets around the world.
One conclusion of this discussion was that the enforcement of the Eco-Design Regulation has lead to the manufacture of lower-loss transformers, where the savings in the total cost of ownership (TCO) are taken as a measure of their cost-effectiveness. In addition to the cost of the transformer, the TCO also includes the capitalized costs of transformer losses (no-load loss and load losses).
Furthermore, this discussion also showed that the wider industry community does not really understand how much the TCO model represents or correlates to the reduction of CO2 emissions due to lower transformer losses, which is an important consideration given that the reduction of CO2 emissions is the founding idea of the Eco-Design Regulation.
In short, what is still uncertain at this point in time is to what extent lower-loss transformers actually contribute to the reduction of CO2 emissions. The issue here follows from the fact that a more efficient transformer is, in reality, a larger transformer (in terms of size) according to the current TCO model. The reason for this is that the application of traditional materials will result in a more cost-effective solution even for a larger-sized transformer than with using high-performance materials, which would reduce the size of the transformer.
So, a more efficient transformer requires a slightly bigger core, which in turn requires using a larger number of core steel sheets. This means that in the manufacturing process more steel sheets needs to be produced, which will increase the emissions of CO2.
A bigger core then requires bigger windings. Additionally, a reduction in load losses is in practice achieved by using a conductor with a larger cross-section, which further increases the amount of copper required for the production of such transformer. So again, in the manufacturing process more conductors will have to be produced, which will increase the emissions of CO2.
With bigger windings, more insulation material is used, which is largely cellulose-based, meaning some more trees will have to be cut down in Sweden, Canada or elsewhere in the world, and processed to get the final product: paper or transformerboard. As this entire manufacturing chain involves some energetically very demanding processes, each increase in the use of materials implies the increase in CO2 emissions. Besides, with every tree that is cut down to help manufacture a larger transformer, there is less absorption of CO2 from the air, which can overall be seen as increasing the levels of CO2.
With distribution transformers, an additional problem is the load capacity of utility poles and supporting structures the transformers are mounted on. Each modification or reinforcement of these structures will lead to additional emission of CO2, which in some cases quite possibly cannot even be compensated for by the reduced emissions due to lower losses. In sum, while the reduction of transformer losses throughout their lifecycle undoubtedly contributes to the reduction of CO2 emissions, there is obviously a whole series of effects which initially increase the emission.
It is interesting to note that during our discussion nobody was able to actually confirm whether these effects are considered while preparing and implementing such regulations. If this is not the case, then the correlation between the TCO model and the actual reduction in CO2 emissions definitely needs confirming, especially considering that the idea of loss reductions has not been entirely explored by the regulations enforced thus far, and this process may be continued in the future requiring further reduction of transformer losses. Considering that these processes have an influence on the entire industry, we have to be certain that we are using the right tools to measure their effects.
If there are readers who have answers to some of the above questions, I would like to hear from you. Any comments or questions regarding this subject are also welcome.
In this issue, we bring you two high-profile interviews – an interview with the chief executive at a European TSO which boasts a European first 400 kV smart substation, and an interview with a general manager of one of the world’s largest manufacturers of tap-changers.
In addition to our regular columns that bring fresh commentary on the latest market trends and topics related to transformer lifecycle, in this issue we introduce a new column dealing with water in transformers. Water in transformers is an intriguing topic and usually attracts an interest of large groups of professionals in the field of high-voltage electrical equipment operation and maintenance. There are many open questions on what seem to be trivial yet complex phenomena when it comes to the presence and effects of water in transformers, and this column will try to address some of them.
A selection of technical articles and advertorials bring presentations on a range of topics including transformer technology, testing and diagnostics, transformer insulation, transformer maintenance and remote assistance, and more.
Feel free to contact us with commentary on any of the topics and issues covered in the magazine, or to express intent to present your research or point of view on any other topic of interest for our industry. For any questions on how to publish your work with us, contact info@merit-media.com.
I wish you a lot of success in the New Year 2019!
Mladen Banovic,
Editor-in-Chief