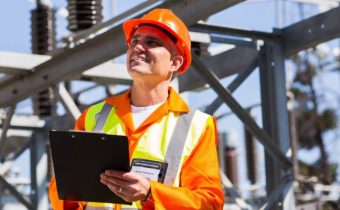
Using computer-aided engineering to enable the digitalisation of transformers
The main challenges in applying virtual twin models and prototypes is the long simulation times that make it difficult to explore designs in development and to forecast scenarios during operation.
by John Wanjiku, Mike Gruetzmacher
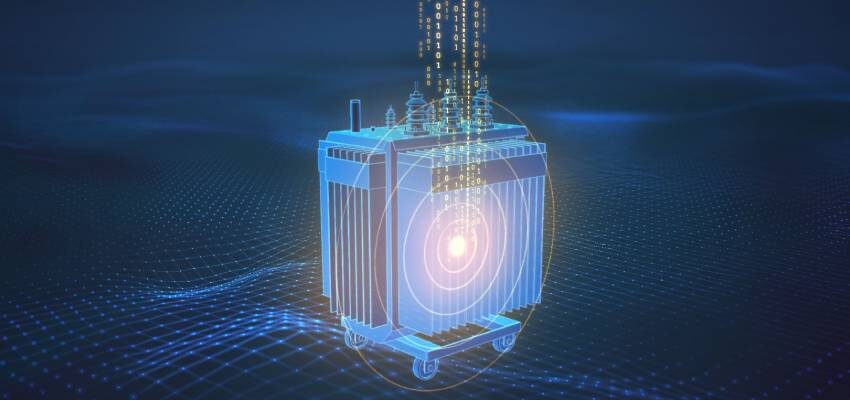
1. Introduction
Major transformer manufacturers have responded to today’s challenges by implementing digital technologies and connectivity provided by “smart” asset management services
The disruption of supply chains by unforeseen events such as pandemics, severe weather events, labour, trade, and political disturbances, affect maintenance, upgrades, and delivery of new transformers. In addition, there is competitive pressure in emerging markets from low-cost suppliers who do not necessarily have to meet the same standards and testing cycles. In mature markets, utilities are operating equipment beyond their life, with reduced maintenance budgets. Additionally, the increase in grid instability attributable to the integration of intermittent renewables, electric vehicle (EV) charging, data centres, and a decline in traditional inertia generation is resulting in more dynamic loading of transformers [1]. Irrespective of the generation and demand changes, transformers are expected to last for decades—30 to 40 years for power transformers.
Major transformer manufacturers have responded to these challenges by implementing digital technologies and connectivity provided by “smart” asset management services. IoT systems, such as the Siemens Sensformer®, and the ABB AbilityTM connectivity features, is enabling the digitalisation of transformers [1, 2]. According to ABB, transformer monitoring can reduce catastrophic failure by 50 %, repair costs by 75 %, and lost revenue by 60 %, while the annual saving of a transformer run with and without monitoring can amount to 2 % of the price of a new transformer [1].
Transformer digitalisation is digitally capturing the transformer development process, from ideation, realisation, to field utilisation to help predict hotspots that are important in forecasting the loading and remaining life
1.1 What is “Transformer digitalisation”?
Transformer digitalisation is digitally capturing the transformer development process, from ideation (design and analysis), realisation (manufacturing and supply chains management), to field utilisation to help predict hotspots that are important in forecasting the loading and remaining life. The main aim is to add revenue opportunities and improve market agility [2]. A holistic transformer digital twin improves reliability and performance, even during extreme natural events by minimising outages through load and asset scheduling.
Simulation- and test-driven development mainly play a major role in the ideation and utilisation phases of the digitalisation process. In the ideation phase, computer-aided engineering (CAE) simulations are leveraged in performance analysis, while reducing over-design and the number of physical tests. This reduces the time to market and costs. In the utilisation phase, as illustrated in Fig. 1, real-time monitoring and feedback from the digital twin are necessary for efficient operation, predicting health and remaining life. Connectivity allows secure data transfer to the cloud, or it can be logged locally. Analysing this data generates actionable information, which is hardware, software, or services related to optimising transformer operation, and condition-based maintenance. Furthermore, unforeseen natural events are mitigated through asset and load scheduling.